
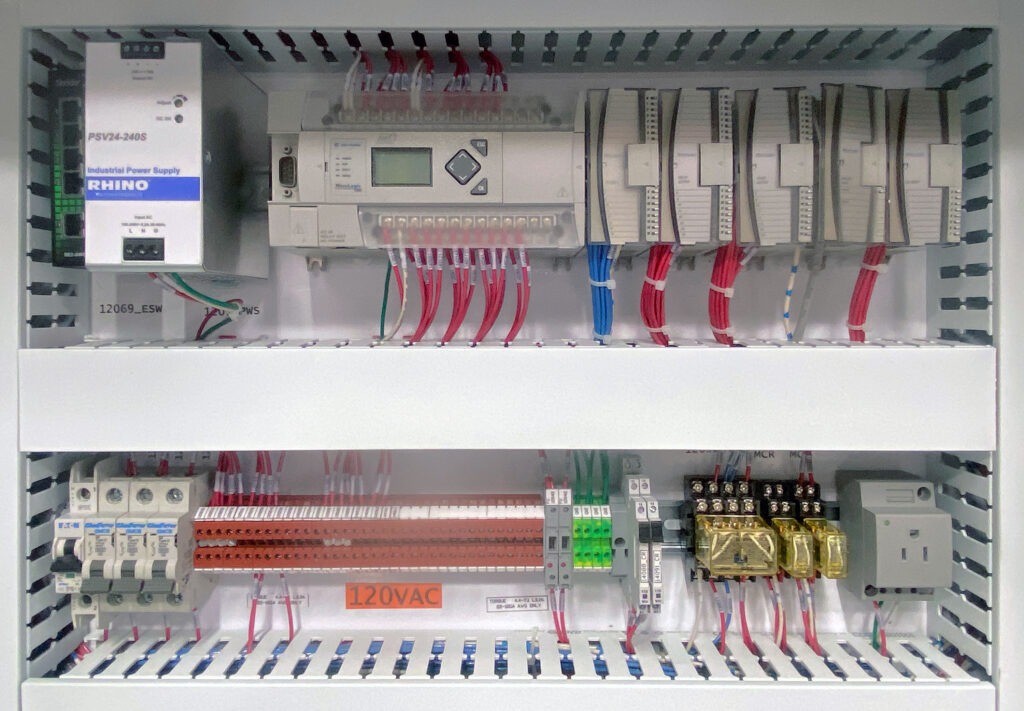
Our PLC programmers squeeze precious efficiency out of your operation.
We have experience in these areas of Automation:
- PLC programming
- SCADA Design
- HMI Development
- Historizing data
- Industrial Reporting
- Industrial IT
As manufacturing facilities around the globe rely heavily on PLCs, the technology continues to evolve. We have expertise in developing, supporting, and managing these systems.
We know how important it is for you to keep your systems running smoothly and we’re here to help. We’ll listen to you and work with you to design the perfect solution for your needs. We’ve helped customers with many tasks including building systems from the ground up for a new facility to retrofitting new PLCs into an older system with no downtime.
USS Automation manufactures our own control panels so we have complete control over every aspect of the design and build. This ensures the highest-quality and lowest-cost for our customers.
Out with the Old, In with the New: A Case Study
A large worldwide chemicals firm that makes plastic pellets hired USS Automation for the important task of retrofitting new modern PLCs into a facility with four product lines controlled by one PLC each.
The PLCs had different characteristics from the old ones that we had to analyze and control for.
If anything didn’t work the moment we turned it on then the company would experience downtime so that was to be avoided.
Old PLC:
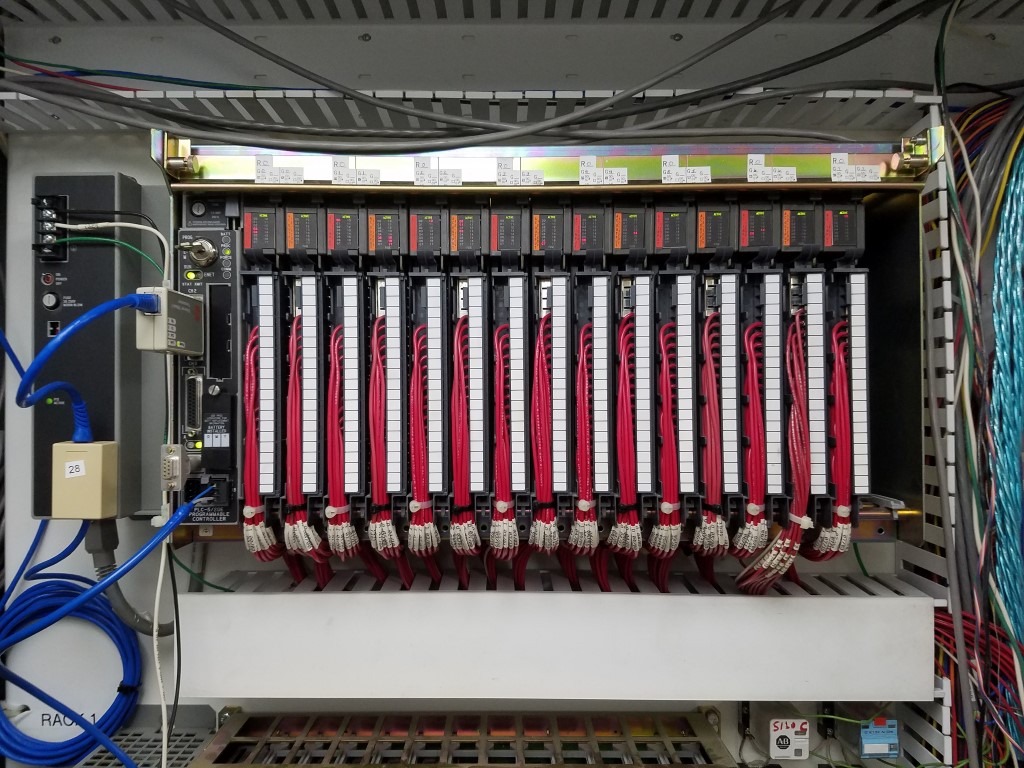
New PLC:
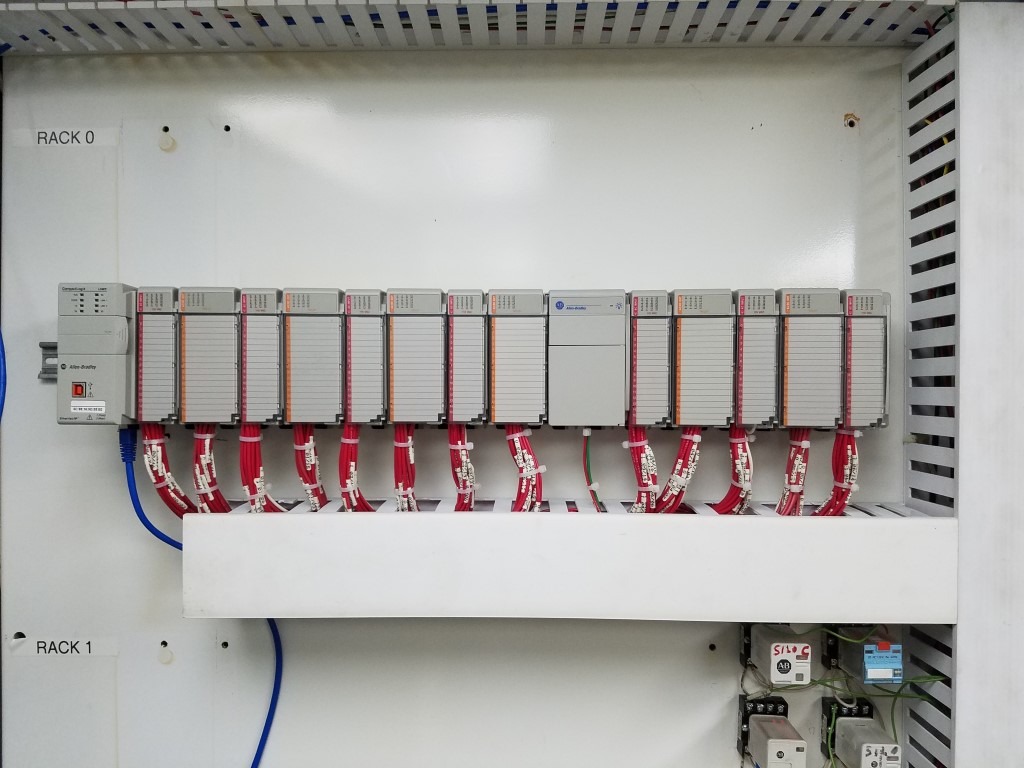
We were also tasked with giving their Wonderware InTouch software a makeover because a large number of links, animations, and graphics had deteriorated and weren’t working from various changes over the decades.
And it all had to be done without changing the underlying programming they use as the batching system to run their facility.
Any hiccup would result in downtime and lost revenue.
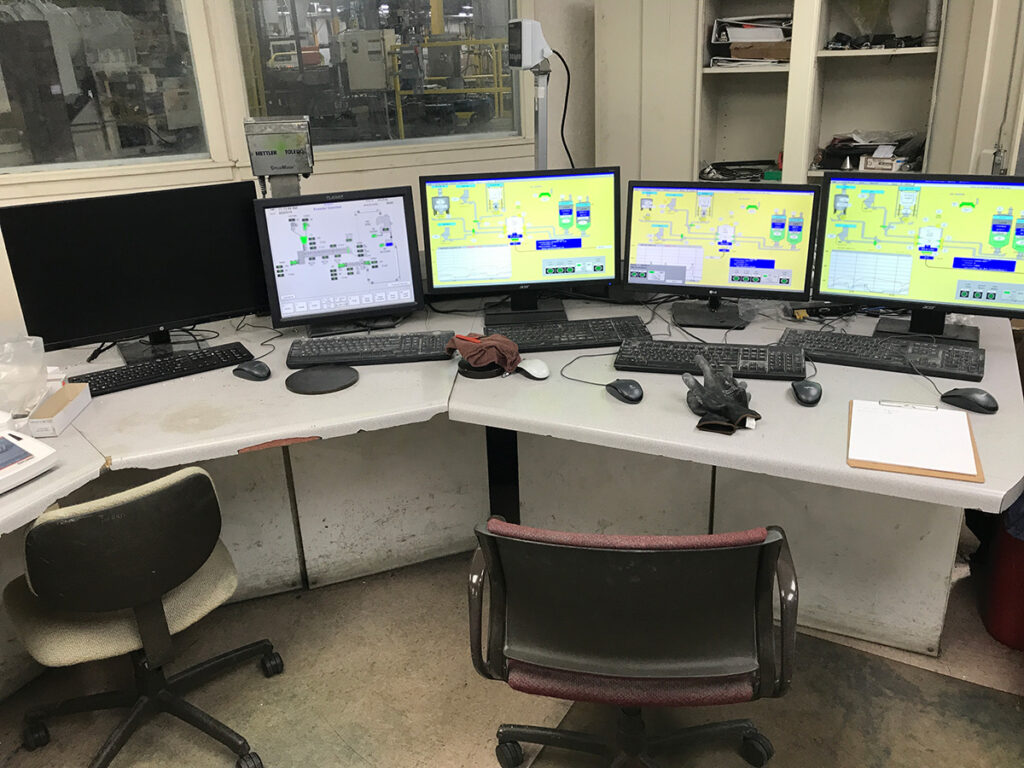
The customer also asked us to install Wonderware Historian to historize their processes. We also configured industrial reporting software so they can analyze the quality of their product.
Oh and in addition to replacing the PLCs we were replacing the PCs that ran the Wonderware systems as well.
This was a large, important project so we split up the effort between our team, began analysis, research, and went to work.
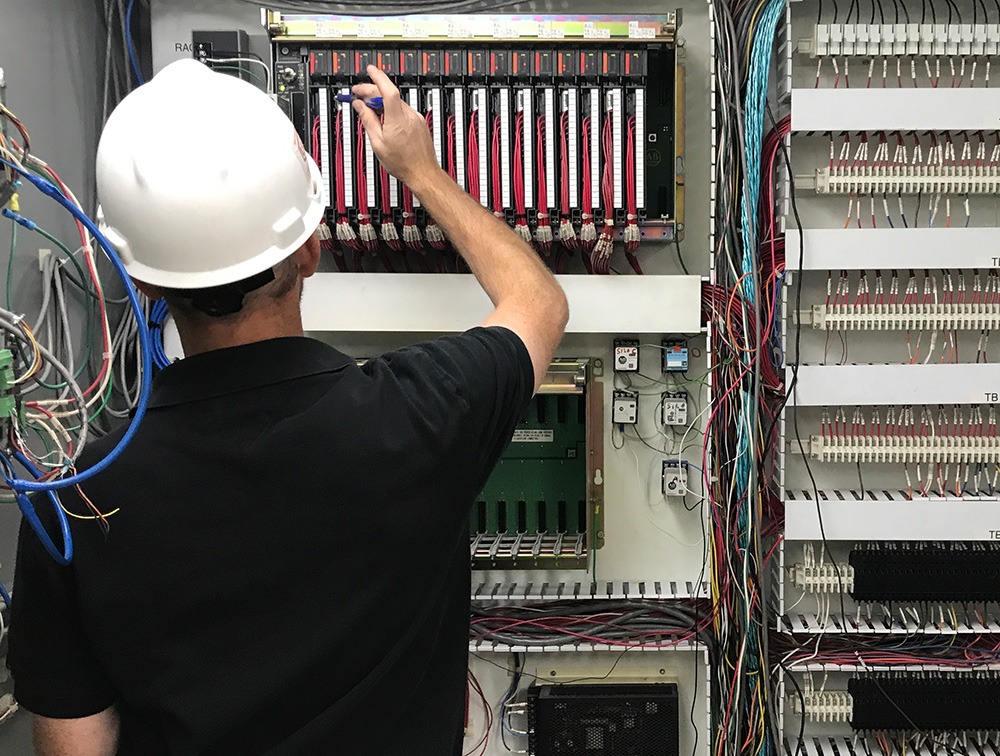
The effort paid off. Once the PLCs were programmed, the PCs were configured, the software refreshed, and the Historian was installed and configured we traveled to the facility to do the physical installation.
We performed the installation of the components over a long weekend while the plant was already in a pre-planned downtime state.
After removing and reconnecting thousands of wires, replacing the PLCs and PCs over the course of two days it was time to switch it on and work out anything else left to do.
We spent the next day getting the software perfected and the entire plant was up and running when the operators showed up for work the day after.
The result was ZERO plant downtime! The feedback from the operators was great…they loved the updated system and management did too.
PLC Cabinet Before:
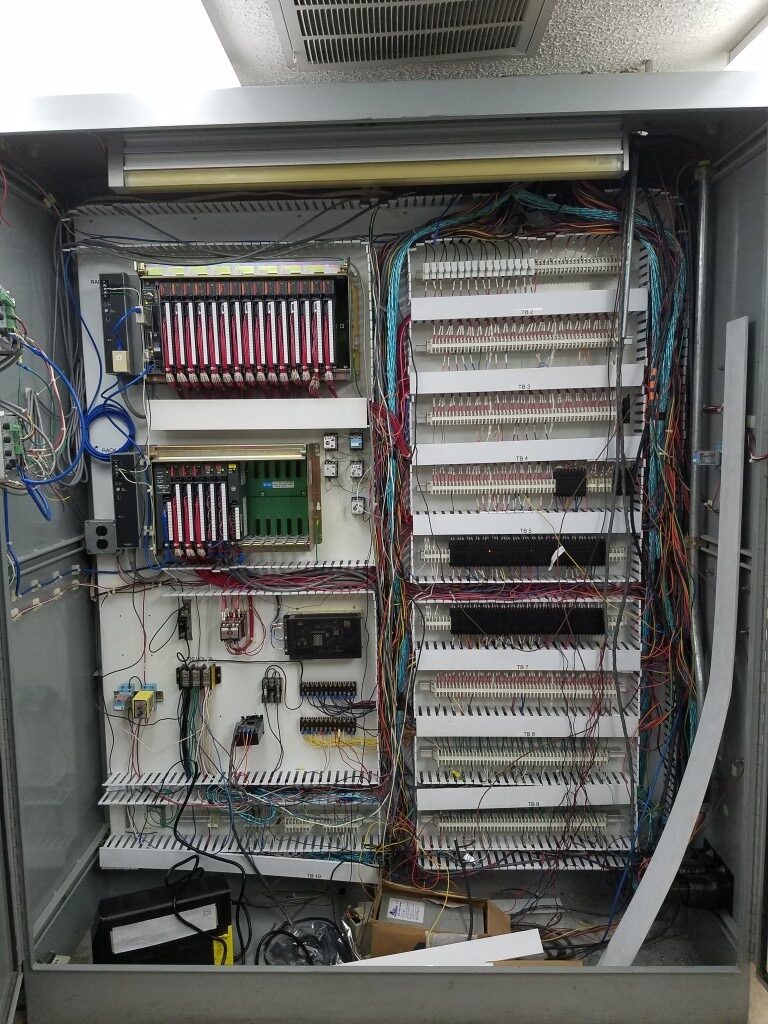
PLC Cabinet After:
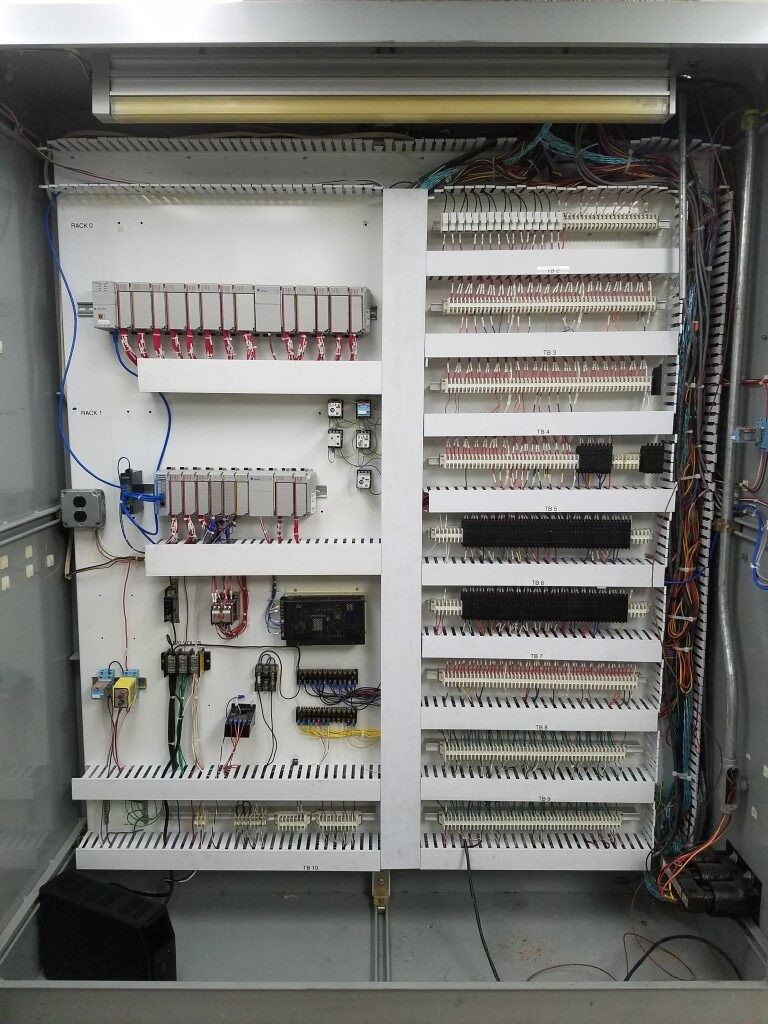